CASO PRÁCTICO: OPTIMIZACIÓN DE LA PRODUCCIÓN DE UNA POLEA
¿Cómo puede ayudarnos la metodología de diseño de producto sostenible a optimizar la producción de una polea? En este caso real, explicamos como se llevó a cabo el proyecto, y como, esta metodología, permite identificar los focos de impacto del proceso, proponer estrategias de mejora y aumentar los niveles de sostenibilidad y eficiencia del producto.
¿CÓMO NACE EL PROYECTO?
El proyecto se centra en una polea plana, que forma parte de la transmisión de una máquina con la función de llevar la potencia entre ejes por medio de una banda elástica (en este link, podéis encontrar más información sobre transmisión por correas).
Ante un aumento de la producción de estas máquinas, se decide llevar a cabo un estudio para optimizar su coste, su tiempo de fabricación y el uso de recursos. Se analizan los componentes que la forman y, entre otros, se escoge esta polea, para su optimización. Ya que, aunque es un componente simple y de tamaño reducido, se montan 12 unidades por máquina, lo que convierte un ahorro pequeño por unidad en un impacto relevante por máquina.
Y se decide aplicar la metodología de diseño de producto sostenible (Figura 1), con el objetivo de estudiar alternativas en su diseño.
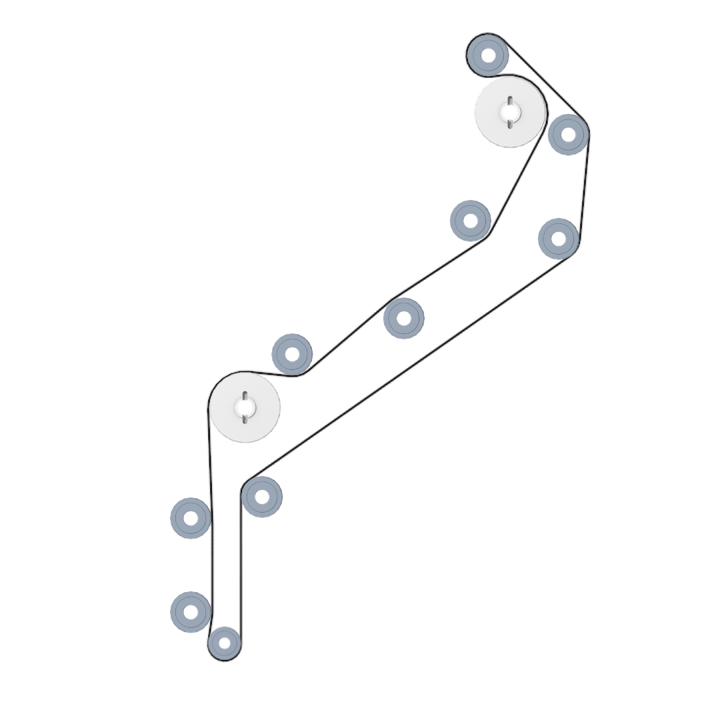
DEFINICIÓN DEL PROYECTO
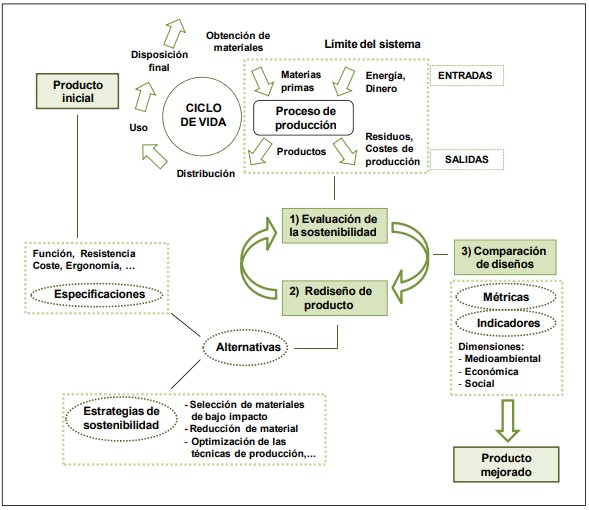
Siguiendo la metodología (Figura 1), comenzamos definiendo el proyecto detalladamente:
Conocer el producto y establecer las especificaciones que debe cumplir
- Marcar los objetivos del proyecto
- Determinar las métricas con las que se medirán estos objetivos
- Obtener los indicadores que definirán el impacto por dimensiones
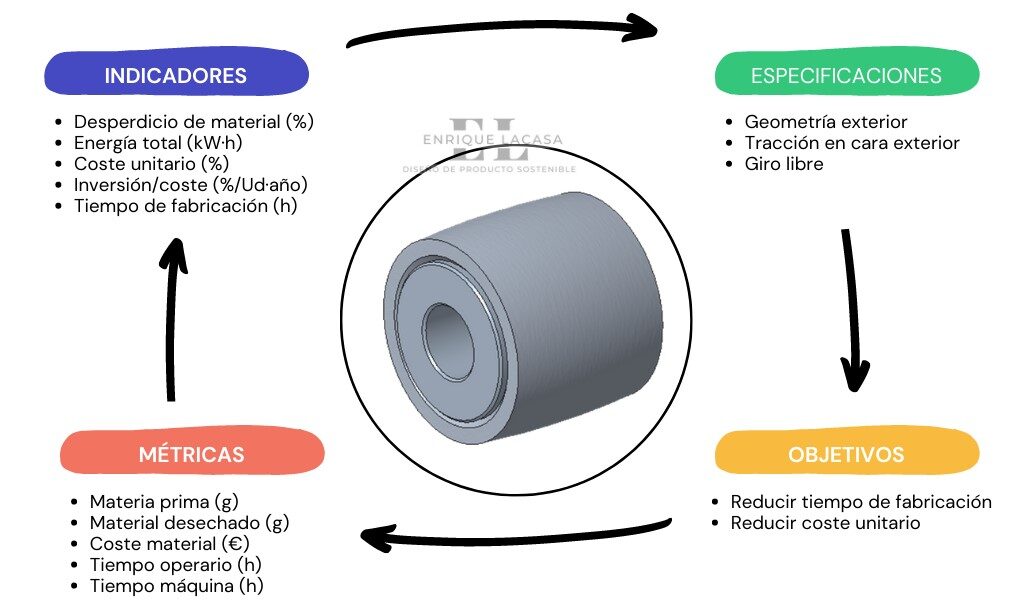
En este caso, la pieza debe mantener la geometría exterior, ya que determina la relación de transmisión, una fricción adecuada en la cara exterior para que no resbale la banda elástica y poder girar libre dentro del eje.
Como objetivos empresariales, se marca, reducir el tiempo unitario de fabricación y el coste total. Para lo cual se definen unas métricas que midan parámetros claves, y unos indicadores que muestren la progresiva mejora, en línea con los objetivos.
ANÁLISIS DEL COMPONENTE
Ahora, vamos a analizar la sostenibilidad de la polea, con el fin de identificar los focos de impacto. Para ello, utilizamos la herramienta de análisis de ciclo de vida.
El sistema de estudio corresponde a la fase de fabricación, desde la entrada de materia prima hasta la salida de la polea terminada. Y se toma como unidad de medida, para la valoración de los datos, 1 unidad de polea fabricada.
La figura 3 muestra el análisis de inventario en detalle, con las entradas y salidas de cada etapa, y en la Tabla 1 se explica.
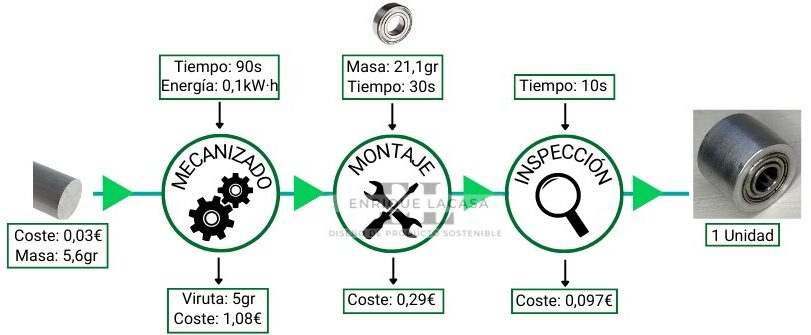
Tabla 1. Descripción del análisis de inventario.
ETAPAS | DESCRIPCIÓN | ENTRADAS | SALIDAS |
INICIO | Se parte de una barra calibrada | Masa del aluminio | Coste del aluminio |
MECANIZADO | Se mecaniza la barra con la | Electricidad Tiempo de máquina | Coste de electricidad Coste de máquina Desechos (viruta) |
MONTAJE | De forma manual, se añaden los 2 | Masa de rodamientos Tiempo mano de obra | Coste de rodamientos Coste mano de obra |
INSPECCIÓN | Se revisa un 10% de la | Tiempo de mano de obra | Masa de desechados Coste mano de obra |
A partir de los datos recopilados en el inventario, se calculan las métricas y los indicadores que definen el perfil de impacto de la polea (Tabla 2).
Tabla 2. Métricas e indicadores, diseño inicial.
MÉTRICAS | ||||
Material (g) | Desecho (g) | Coste material (€) | Tiempo máquina (min) | Tiempo operario (min) |
26,7 | 4 | 0,035 | 1,5 | 0,67 |
INDICADORES | ||||
Desperdicio (%) | Energía total (kW·h) | Coste unitario (€) | Inversión (€/Ud·año) | Tiempo total (min) |
15 | 0,1 | 1,5 | 0 | 2,17 |
Tras el análisis de los datos, se identifica como principal foco de impacto, el proceso de mecanizado, ya que:
- El material desperdiciado es de un 15%
- El coste de la energía aporta el 72% del coste total (1,5€)
- El tiempo de máquina (1,5 minutos) corresponde al 69% de todo el tiempo de fabricación
PROPUESTA DE ALTERNATIVAS
Este caso es un poco particular, debido a que, a partir del cambio adoptado para optimizar el proceso de mecanizado, se identificó otra alternativa de mejora. Esto nos demuestra que el diseño, es un proceso muy dinámico.
Así pues, inicialmente, se puso el foco en la mejora del proceso de fabricación, analizando diferentes propuestas (Tabla 3). Pero, rápidamente, se viendo claramente, que la mejor opción era fabricar la polea por inyección de plástico.
Tabla 3. Propuestas de mejora.
ALTERNATIVAS |
VENTAJAS |
INCONVENIENTES |
Mecanizado en POM |
· Facilidad de mecanizado · Reducir el consumible · Reducir coste de consumible y energía |
· Se mantiene el % de desecho · La reducción en coste y tiempo es muy pequeña |
Cambiar materia prima, partir de tubo para reducir el mecanizado |
· Reducir material desechado · Reducir tiempo de mecanizado · Reducir coste de fabricación |
· Se mantiene el coste debido a que la materia prima es más cara |
Fabricación por inyección de POM |
· Se reducir el coste · Se reduce el tiempo de fabricación · Se reduce el material desechado |
· Se requiere inversión inicial · Dudas sobre la fricción en la cara exterior |
El siguiente paso, es profundizar en el análisis de la propuesta de mejora definida, para comprar los datos con el diseño inicial (Tabla 4) y determinar, de forma objetiva, que realmente se consigue una mejora.
Para la fabricación por inyección se toma el POM debido a que es un material ampliamente utilizado para componentes de transmisión, por su baja fricción y alta resistencia al desgaste.
Tabla 4. Comparativa de las alternativas de mejora.
MÉTRICAS |
DISEÑO ACTUAL |
PROPUESTA |
VARIACIÓN |
Proceso de fabricación |
Mecanizado |
Inyección |
– |
Material |
Aluminio |
POM |
– |
Materia prima (g) |
5,6 |
2,8 |
-50% |
Material desechado (g) |
4 |
0,2 |
-95% |
Coste material (€) |
0,035 |
0,022 |
-37% |
Tiempo máquina (min) |
1,5 |
0,3 |
-80% |
El análisis comparativo se realiza a través de las métricas (no se toma la métrica de tiempo de operario al ser la inyección un proceso automatizado). Donde, todas ellas, muestran una mejora muy notable.
Y, en este punto, es cuando surgió la segunda alternativa de mejora: eliminar los rodamientos. Una vez decidida la fabricación en POM, vimos la posibilidad de que la propia polea girara loca sobre el eje sin necesidad de otros componentes (rodamientos), aprovechando la propiedad de baja fricción del POM.
A priori, representaba una gran mejora, ya que eliminamos un proceso de la cadena (montaje) y el añadir dos componentes (rodamientos). Pero, era un cambio significativo en cuanto al funcionamiento de la polea, con lo que había que verificar la viable técnicamente de la solución.
Para lo que fue necesario prototiparlo y montarlo en varias máquinas, para hacer test de comportamiento y durabilidad. Se optó por fabricar los prototipos en POM mecanizado, y estas muestras, pasaron los test.
La metodología de diseño de producto sostenible, tiene un enfoque de mejora continua, con los cual, se podrían aplicar los siguientes pasos de forma continuada:
- Rediseñar la polea con una nueva propuesta
- Calcular métricas e indicadores y compararlos con los ya obtenidos
- Volver a identificar focos de impacto y buscar alternativas
Con lo cual, el proceso de montaje de los rodamientos hubiera aparecido como foco de impacto tarde o temprano. Pero al detectarlo en esta primera iteración, conseguimos ahorrar pasos.
ANÁLISIS DE LA MEJORA
Una vez tenemos la propuesta de diseño de mejora: polea fabricada por inyección, en POM, y sin rodamientos. Se vuelve a calcular el impacto en sostenibilidad mediante la herramienta de análisis de ciclo de vida sobre el nuevo sistema.
La Figura 5 y tabla 5 muestran el análisis de inventario del proceso final y la Tabla 6 las métricas e indicadores obtenidos.
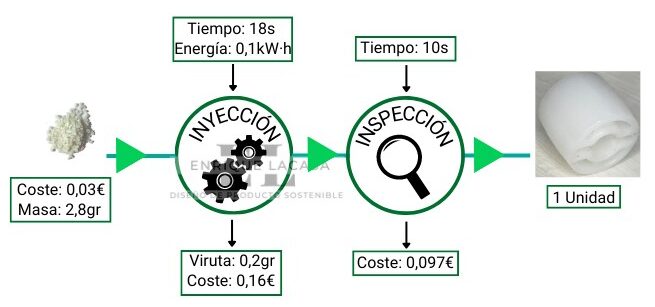
Tabla 5. Descripción del análisis de inventario.
ETAPAS | DESCRIPCIÓN | ENTRADAS | SALIDAS |
INICIO | Se parte de granza de POM | Masa del POM | Coste del POM |
INYECCIÓN | Se inyecta la polea a razón de 4 unidades por inyección | Electricidad Tiempo de máquina | Coste de electricidad Coste de máquina Desechos (Defectuosas) |
INSPECCIÓN | Se revisa un 10% de la producción | Tiempo de mano de obra | Masa de desechados Coste mano de obra |
Tabla 6. Métricas e indicadores, diseño final.
MÉTRICAS | ||||
Material (g) | Desecho (g) | Coste material (€) | Tiempo máquina (min) | Tiempo operario (min) |
2,8 | 0,2 | 0,022 | 0,3 | 0,17 |
INDICADORES | ||||
Desperdicio (%) | Energía total (kW·h) | Coste unitario (€) | Inversión (€/Ud·año) | Tiempo total (min) |
7 | 0,1 | 0,2 | 0,875 | 0,47 |
COMPARATIVA
Como último paso de la aplicación de la metodología, vamos a comparar las métricas e indicadores del caso inicial y del nuevo diseño, para ver la variación de los parámetros del sistema.
Se realiza la comparativa (Figura 6) en términos porcentuales por dos razones.
- Unificar la unidad de medida, para tener una comparativa conjunta de todas las métricas e indicadores.
- Ver realmente la variación obtenida y su magnitud.
En el gráfico, se toma 0% como no variación y 100% como eliminación total de ese parámetro. Así, tanto en las métricas como en los indicadores podemos ver una mejora en línea con los objetivos de reducir el coste y el tiempo de fabricación.
- El coste del material se reduce un 37%
- El coste total de la polea se reduce un 86%
- El tiempo por operario se reduce un 74%
- El tiempo de máquina se reduce un 80%
- El tiempo total de fabricación se reduce 78%
Además, se han obtenido otras mejoras en el proceso:
- Se reduce el material desechado en 95%
Por contrapartida, la energía total empleada en el proceso se mantiene y aparece una inversión inicial necesaria para la fabricación del molde. Es necesario tener en cuenta las unidades necesarias de este producto para valorar la viabilidad económica de esta inversión.
Así, durante el primer año de producción del nuevo diseño, se tendría, por un lado, el coste unitario de la pieza (0,20€) y por otro, el coste en inversión del molde por unidad (0,875€). Lo que representa un coste total de pieza de (1,075€), menor que el coste inicial de 1,50€.
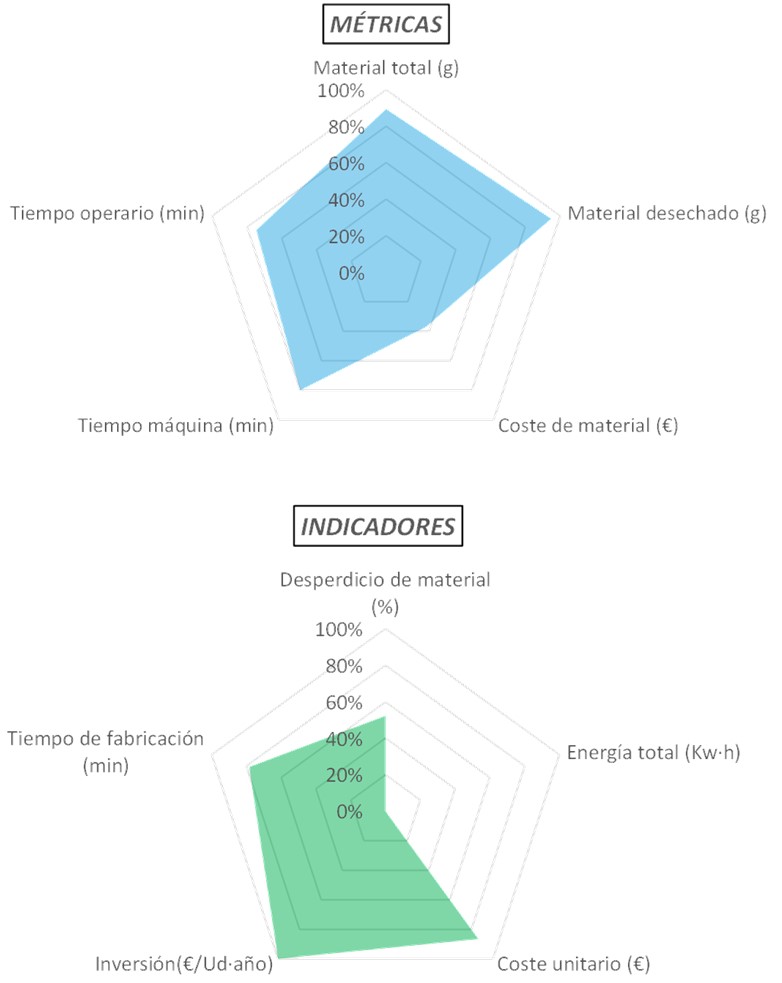
¿QUÉ BENEFICIOS APORTA LA APLICACIÓN DE ESTA METODOLOGÍA?
Es obvio, que las mejoras obtenidas en este caso real, han sido muy grandes, no es lo normal mejoras del 70%, 80% o 90%. Pero, al ser un componente pequeño, es normal que se descuide su optimización durante el diseño, y que tenga un rango de mejora como el que hemos visto.
De todas formas, se demuestra el potencial de mejora que puede aportar aplicar esta metodología. Ya que se ha conseguido una mejora significativa en una pieza, a priori, muy sencillo en diseño y en fabricación.
Este artículo muestra los pasos a seguir en la aplicación de esta metodología y nuestra manera de ponerla en práctica:
- Conocer bien el producto y el sistema
- Medir y analizar los datos
- Tomar decisiones en base a los resultados